Här får du vara med om hur en Trio 80 blev till.
En tidningsartikel i Båt för Alla -80 om att själv bygga sin " dröm båt" genom alla de självbyggarvarven som fanns runt glada 80-talet.
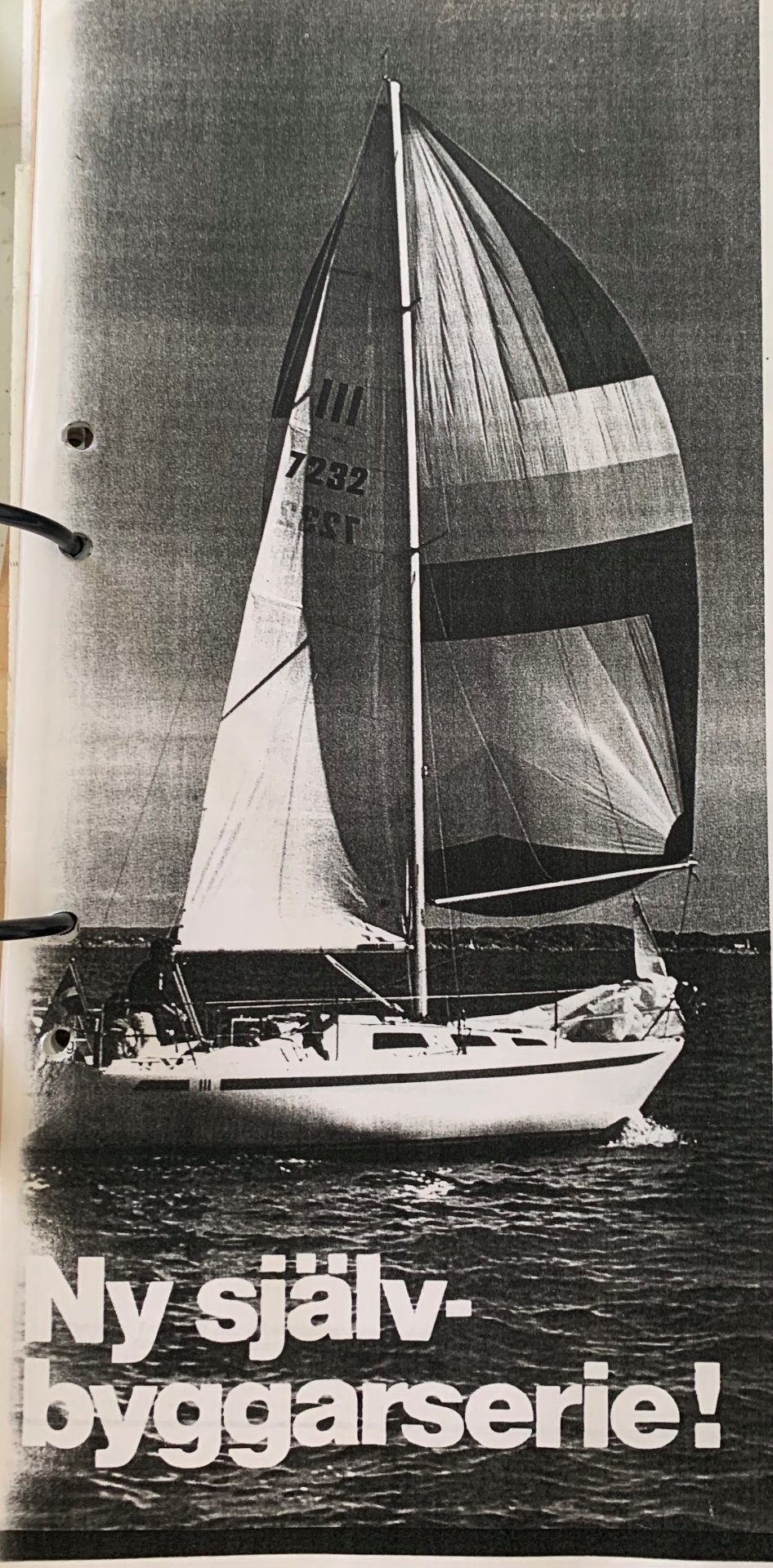
Tidningsreportage: Någon gång i början av 80-talet i Båt för Alla.
Här startar en ny självbyggarserie i Båt för alla, den sjätte i ordningen. Bygget är det största i glasfiber som vi på tidningen hittills givit oss i kast med. Självfallet är serien som allra intressantast för dem som funderar just på att bygga just en Trio 80, som vi valt, men det mesta av det som behandlas är lika giltigt för andra självbyggen i glasfiber. Seriens sju avsnitt är ägnade åt var sitt special område. Först behandlas plastjobben, sedan inredningsarbeten, motorinstallation, el dragning, osv.
Byggreportage: Janne Lundbladh. Båt för alla.
Expertgranskning plastningsavsnittet. Lennart Blomstergren .
Trio -Båtar AB.
Återberättat: Patrik Karlekvist. Hemsidan Trio 80.nu
Inledning.
Många stockholmare har under det här båtbyggandets gång frågat mig hur det kommer sig att jag, bosatt i Stockholmsområdet valde det många gånger obekväma alternativet att resa till Göteborg för att bygga båt, när det finns så många självbyggen att välja på med betydligt närmare håll. Och varför valde du en så okänd och på ostkusten sällan sedd båt som Trio 80?
Modern men traditionell.
Svaret på frågan, varför det blev en Trio 80 som den här byggserien är uppbyggd på, och ..!?
Härifrån har texten försvunnit på reportaget tyvärr. Men delen om hur och vad man skall tänka på vid plastningen av båten följer nedan.
Hoppas du ändå får en intressant läsning.
Bra förberedelser = ett bra självbygge.
Allt börjar från början, med en gelcoatform, några fat med plast och ett antal rullar glasfiber, som efter mycket arbete, tillsammans så småningom förhoppningsvis blir till det önskade arbetet, är för många den enda möjlighet till förverkligande av båtdrömmarna. Trots att självbygget inte alltid blir ekonomiskt fördelaktigt för byggaren som han kanske från början tänkt sig så är det här sättet att skaffa båt avsevärt mycket billigare än något annat, och därför har det också blivit allt populärare med åren och det med allt kärvare kreditläge. Idag finns någonstans mellan 20 och 30 "självbyggarvarv" runt om i Sverige, och de svarar årligen för att vår fritidsflotta utökas med mellan 300 till 350 båtar ( år 1980)
Att välja självbyggebåt.
Inte bara båten.
I den del av "båtsalongen" som finns med i detta nummer av Bfa, fanns vid denna tiden de allra flesta svenska självbyggarvarv representerade. Vilken av dem som en presumtiv byggare valde, beror på en rad av både rationella och irrationella orsaker, som tycke och smak, bankkontots storlek och bankkamrerens välvilja till lån och på rikets geografi.
Många byggare väljer sin båt, därför att den färdiga produkten som de utgått ifrån, i en valsituation svarar något så när mot deras båt dröm och plånbok. Alltför ofta träffas det utan att den blivande båtägaren vare sig besökt byggplatsen eller satt sig in i byggmetodiken eller arbetsmiljön, något som borrar för en hel del överraskningar och för det mesta tyvärr av det tråkigare slaget.
En checklista
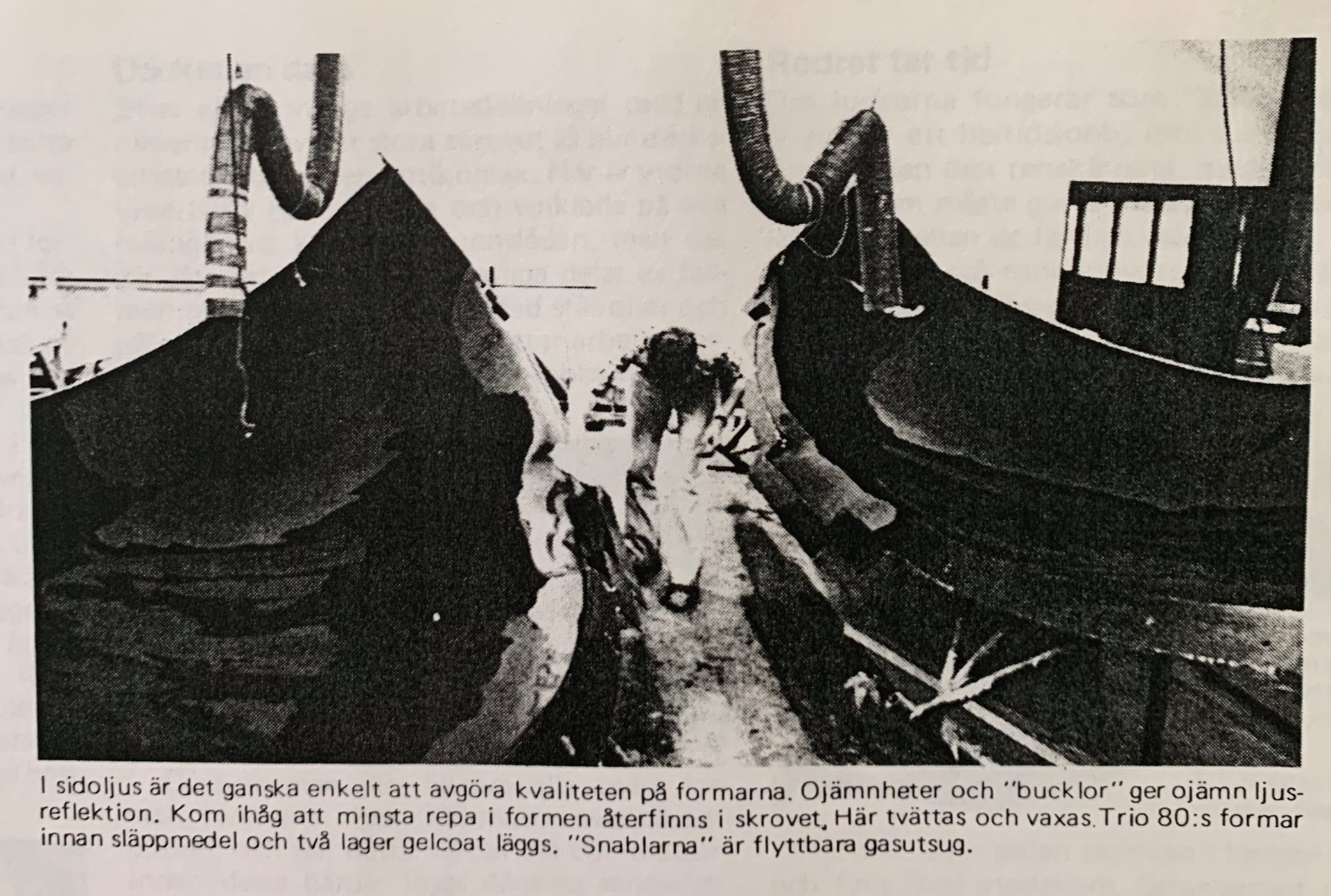
När det blir dags för båtbyggaren att ta en ordentlig titt på bygglokaliteterna och slutligen bestämma sig för att om han skall ge sig in i det stora företaget att själv bygga båt, så bör han således kontrollera följande.
- Är formarna för båten i ett sådant skick att skrov-, däck-, och detaljfinish blir av professionell klass?
- Läggs gelcoaten av varvspersonalen?
- Är formarna utformade på ett sådant sätt att det går lätt att komma åt och att jobba med och inne i dem?
- Är arbetsmiljön acceptabel?
- Tillhandahåller varvet alla verktyg som behövs?
- Vilka kvantiteter matta och plast ingår i byggpriset? Räcker materialet till?
- Vilken experthjälp kan bag vänta mig?
- Vad ingår i priset "plastfärdig båt"?
- Finns all övrig standardutrustning att köpa genom varvet? Till vilket pris?
- Om varvet ligger långt hemifrån, finns övernattningsmöjligheter under byggtiden?
Arbetsmiljön.
På den miljö som den professionella båtbyggaren tillbringar sin arbetsdag i ställs denna under mycket stränga krav från arbetsskyddande myndigheter. Som när det gäller plastning, till exempel så får luften i lokalerna inte innehålla styrengaser till ett högre värde än 50 PPM. Dvs. En viss volym styrenpartiklar per kubikmeterluft.
Motsvarande miljökrav ställs dock ännu inte på självbyggaren, även om mycket talar för att bestämmelserna kommer att skärpas. Att en person under kort tid utsätts för styren gas är naturligtvis minder farligt än kontinuerlig styrenpåverkan. Trots detta är det viktigt att det finns gasutsug och ventilation vid plastningsstället. Om sådan saknas blir det svårare att jobba kontinuerligt med plastning av stora ytor som t.ex. skrov och däck. Om ventilationen i lokalerna är dålig kan detta också innebära att den som jobbar med båtinredning, motorinstallation eller annat drabbas av obehag när andra plastar.
En snygg och något sånär dammfri lokal är ett klart plus. I mycket dammiga lokaler blir det ofta nödvändigt att göra rent t o m ett mindre dygnsgammalt laminat för att nästa lager plast och matta skall fästa hundraprocentigt. Har varvet riktiga omklädnings möjligheter, lunchrum och duschrum så är det en stor fördel. Tänk på att du kommer att tillbringa kanske 100 timmar på den nya " arbetsplatsen" och på att glasfiber och slipdamm kan vara irriterande påträngande. Inte minst när det tas med hem.
Formarna.
En absolut förutsättning för en professionell finish på båten och därmed ett bra andrahandsvärde är goda formar. En okulärbesiktning i sidoljus visar obönhörligen upp ojämnheter, repor och matta partier i formen och varje brist i formen går igen på båtskrovet. En annan förutsättning för hög och stark finish är att formarna rengörs noggrant efter varje användande och att de vaxas omsorgsfullt. Likaså krävs det att gelcoatskiktet - plastbåtens tunna "ytterhud"- läggs på av kunnigt folk, så att skiktet blir tillräckligt tjockt och jämnt.
Formarna skall vara lätta att handskas med, stumma vid varje beröring och utformade så att man direkt, eller med hjälp av långskaftade rollers utan större svårigheter kommer åt överallt. Det är fördel om man slipper jobba inuti formen vid plastning, men det går inte att undvika i stora skrov som byggs i ett stycke.
Material och verktyg.
Det vanligaste vid självbygge är, att byggaren betalar antingen för formhyra och material fram till segelfärdig båt. När det gäller moderna konstruktioner där däck och skrov oftast sätts samman med hjälp av en relingslist i aluminium, kan det vara på sin plats att kontrollera att även denna ingår i köpet.
Kontrollera också hur stora mängder plast och glasfibermatta som ingår i" köpet". För att få reda på om kvantiteterna är generöst tilltagna bör du prata med någon byggare som plastat färdigt. Skulle det uppstå brist på material är det dessutom en fördel att redan från början veta hur mycket man får betala för extra matta eller plast. Är det varvets egna eller marknadspris t.ex.
Nästan alla självbyggarvarv håller med en komplett verktygsutrustning. I denna ingår självfallet också de påläggare och rollers som behövs för plastarbetet. Det kan emellertid vara bra att veta hur " vapenvården" sköts på varvet. Har var och en sin egen utrustning eller är den gemensam. Den "egna" är att föredra.
Experthjälp
Att bygga sin första plastbåt på rätt sätt klarar ingen av utan god handledning. Den handledningen består självbyggarvarvet med. I vilken utsträckning, det bör man ta reda på innan man bestämmer sig för "köp". Ofta brukar det skrivna kontraktet innehålla uppgifter på att vissa timmar handledning, men bästa sättet att ta reda på hur den handledningen fungerar är, att tala med sådana som byggt båt tidigare på varvet. Det är mycket värt att kunna be om råd när man är osäker på om man gör rätt.
Att tänka på innan bygget börjar
Tidsaspekten
Var och en som ger sig in på att bygga båt bör ha klart för sig från början, att han ger sin in i ett företag som är flera nummer större han i sin vildaste planering tänkt sig. Att bygga en båt från början till slut medför både bekymmer och orosmoment som tidigare varit nästan helt okända. Byggandet ger både huvudvärk, onda ryggar, hudirritationer och ett försummat umgängesliv. Samtidigt är det en av de roligaste och mest meningsfulla sysselsättningen som man någonsin ger sig in i. Båtbyggandet är ett företag som i nio fall av tio tar betydligt mer tid i anspråk än planerat och beräknat. Har man bara klart för sig så har man alla möjligheter att nå ett gott resultat. Det lönar sig inte att spika datum. De håller sällan
Plasta aldrig ensam
Uppmaningen har inget med styrengasens farlighet att göra. I stället betyder den, att det krävs minst två man för att uppnå en acceptabel effektivitet vid plastandet av skrov och överbyggnad. Tre man är ett bra plastningslag. En lägger på plast och mattor, en stålrollar ut materialet och en servar med mattbitar och färdigblandad plast. Kan man inte få hjälp under de dagar som krävs för plastjobben så skall man inte ge sig in i ett båtbygge. Den hyrestid för formen som varven sätter ut är inte längre än att två man ofta har fullt schåå att klara denna tidsgräns. Bestäm i god tid med släkt och vänner, så de är lediga under plastningstiden.
Besök varvet innan.
En god tumregel för den som skall välja självbyggnadsobjekt är, att han alltid skall besöka och undersöka "sin" båts bygglokaler innan han bestämmer sig för båten i fråga. Det är nämligen långt ifrån bara båttypen som sådan, som bestämmer slutresultatet av bygget skall bli en framgång eller flopp.
Än viktigare är bygglokalernas utseende, kvalité och finish, kvalitet på plast och glasfiber, och kvantitet som får disponeras, hur lätthanterliga formseten är, varvets skötsel och hållande av material och verktyg, vilka utsugningsanordningar som finns i anknytning till plastningsstället och inte minst, vilken experthjälp som självbyggaren kan räkna med och har rätt att kräva under byggets gång. Det är med andra ord en rad viktiga faktorer som måste ingå i bedömningen av ett självbyggeprojekt.
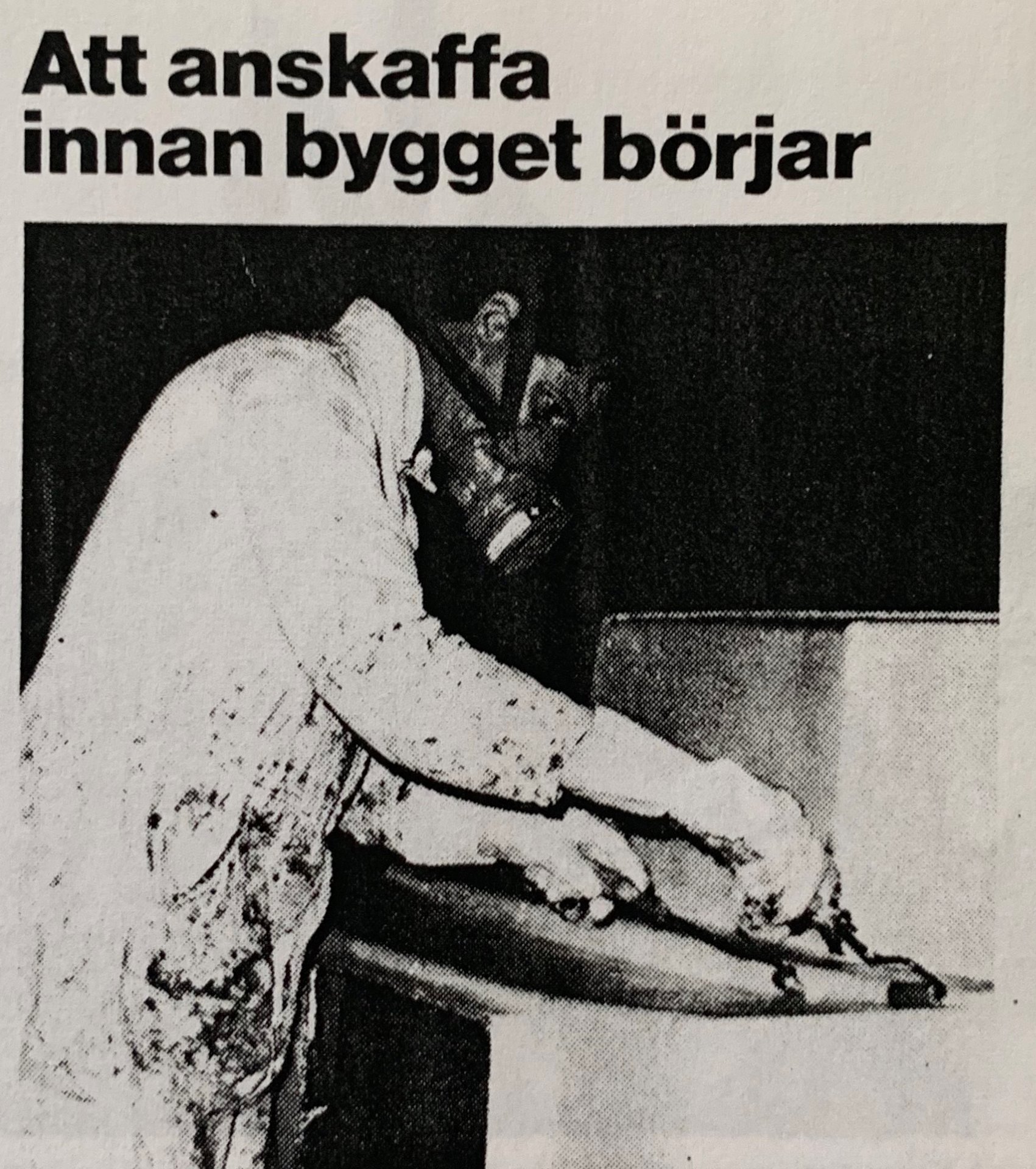
Skyddskläder
När du väl har bestämt dig
för att börja bygga båt ett år, så gäller det att hålla i gamla skjortor, jeans
och skor och lägga dem på lager för framtida bruk, dvs att använda som
"plastkläder", istället för att slänga dem. Efter ett skrov eller en
överbyggnad är kläderna färdiga för soptunnan. Bästa plastningsplagget är en
ordentlig arbetsoverall (byggfirmorna säljer billiga korttidsoveraller), skor
som är släta undertill (så plast och glasfiber får svårt att fästa) och en tunn
mössa av reklamtyp. Skjortor, strumpor och underkläder av nylon och ren
konstfiber är förkastliga. Minsta statisk laddning får glasfiberdamm - att
ställa sig på högkant vilket både är obehagligt och ger hudirritationer. Skaffa
gärna några tuber hudkräm att ha på varvet. En insmörjning med skydd Petrogard
Extra gör huden mindre känslig och lättare att göra ren.
Skyddsmask
Ingen plastning bör ske utan skyddsmask. Det finns flera olika masktyper i marknaden. Själv har jag använt den kraftigaste typen av halvmask med ett skyddsfilter. Den kostar en bit över 100 kr inkl. filter som räcker "en båt ut". Det finns också en något billigare version med två filter, Skyddsfiltren finns det flera typer av, men det som används är et s.k, A-filter. Pris 25 kr. Munskydd är odugliga vid plastning eftersom de inte skyddar mot styren gaser.
Handskar
Många båtbyggare föredrar att jobba i engångs handskar av sjukhustyp. Själv föredrar jag skyddshandskar i PVC med lång krage eller rejäla hushålls handskar av vanligt gummi. De senare typerna måste visserligen göras rena i aceton efter varje användning, men de ger betydligt bättre grepp och håller bättre mot glasfiberstick.
Pris per hanskpar 5-10 kr/st.
Plastningsverktyg
För att klara av plastningen av en normalstor båt krävs faktiskt ingen komplicerad verktygsutrustning. Normalutrustningen utgörs av två eller tre olika typer av stålrollers för utrullning av laminatet, dvs den plastindränkta glasfibermattan, en stor och en liten påläggnings roller av lammull, mohair eller konstfiber, ett par penslar för svåråtkomliga ställen, en vass hobbykniv för kantskärning, nerskärning och skärning av glasfibermatta samt en skrapa för rengöring av plastpåläggningsrollers, kostnad för en komplett utrustning ca. hundralappen.
Byggmaterialen
Grundmaterialen för
båtbygget är glasfibermatta, polyesterplast med accelerator och härdare. Till "basvarorna"
hör också diverse distansmaterial samt gelcoat - det tunna men hårda ytterhud på
båten- och toppcoat, dvs den "plastfärg"
som är på de invändiga ytorna när
inredningsarbetet är slutfört. Toppcoat och gelcoat är s.k. isoftalsyrapolyester
och bägge innehåller som regel accelerator. Den senare krävs för att plasten så
småningom skall kunna härda när peroxid dvs. härdare tillsätts. Dock säljs det
polyester utan accelerator, något som man bör vara uppmärksam på om man själv
köper plast direkt från ett lager.
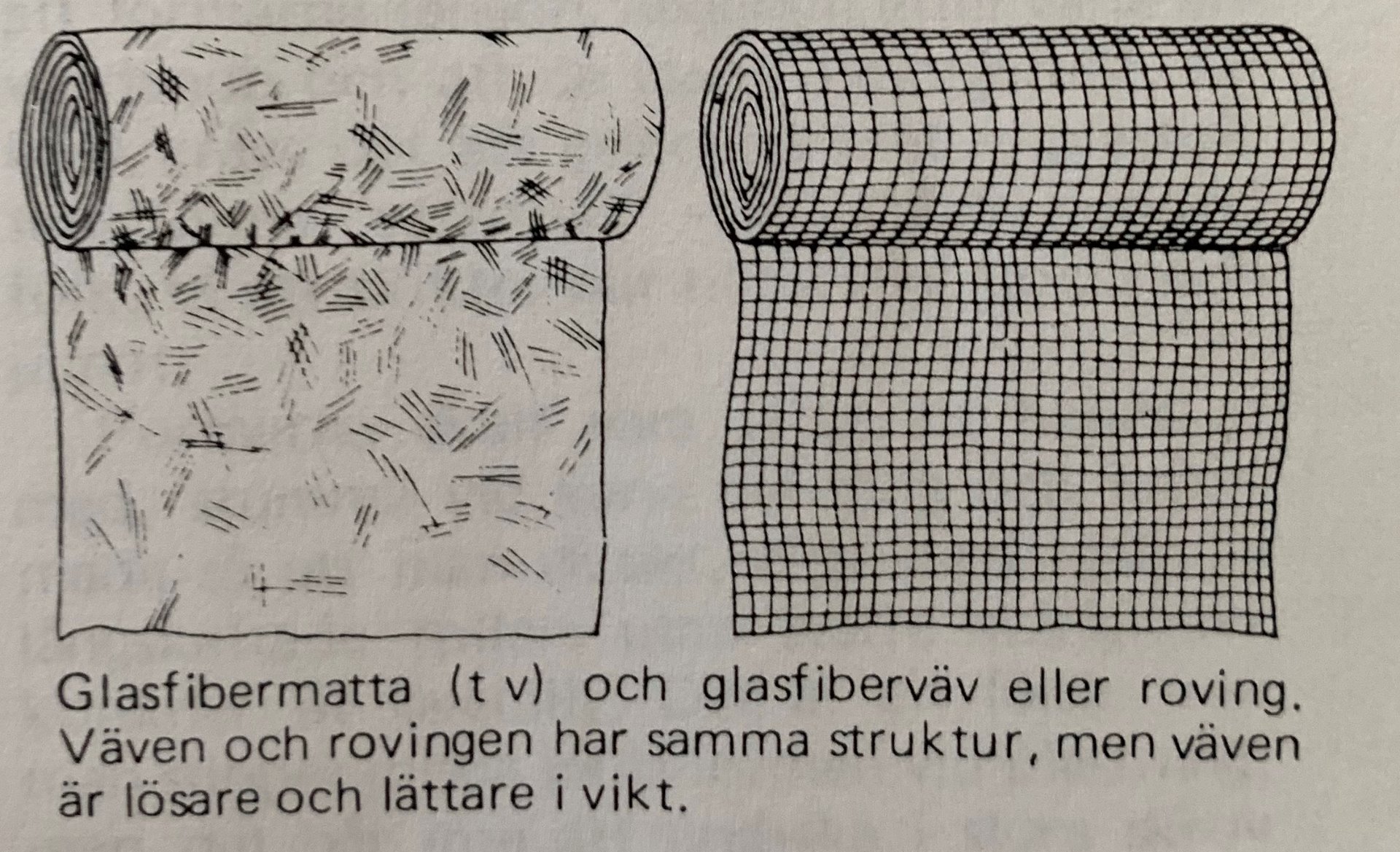
I dag byggs de allra flesta självbyggen i s.k. "miljöplast", dvs. polyester med tillsats av vaxlösning. Där vaxet går under härdningsprocessen upp och lägger sig på ytan och detta förhindrar alltför hög avsöndring av styren gas. Det blir lättare att hålla en god arbetsmiljö. Miljö plasten har blivit boven i dramat när det gäller s.k. delamineringar, dvs när ett laminatlager delar sig i flera skikt vid mekanisk åverkan. Därför har de stora polyestertillverkarna (i Sverige framför allt Jotun och Syntes) utfärdat noggranna regler om hur man skall jobba med miljöplast. Det är en fördel att lägga lagren av plast och matta vått-i-vått, men där detta är omöjligt bör man fortsätta arbetet på laminatet inom 24 timmar efter det att föregående plast/matta är lagd. Plastar men på ett mer än dygnsgammalt laminat bör detta sandpappras och aceton tvättas för maximal vidhäftning. En riktigt använd miljöpolyester ger då ett fullgott plastningsresultat.
Den glasfiber som ger skrovet dess seghet och styrka finns dels som matta eller väv. Glasfibermattan finns i bredder på upp till 1250 mm och i flera olika gramvikter, varav de vanligaste är 300, 450 och 600 g/m2. Som förstärkning i skrov, för det mesta under, men även över vattenlinjen används ibland glasfiberväv eller roving väv. Bägge har varp och vävs på samma sätt som textilier. Glasfiberväven har en gramvikt på 154g/m2 och rovingen finns från 280 - 600g/m2.
Det vanligaste distansmaterialet för däcks- och skrovuppbyggnad
är divinycell, balsaträ och bonocell. Samtliga används för att ge däckskonstruktioner
ökad styvhet och bidrar samtidigt till att hålla nere kondensen.
Distansmaterialet används också i skrovkonstruktioner, men det senare är mindre
vanligt.
Plastningen kan börja!
Vi är två man som kliver in genom dörren till Triobåtars moderna lokaler i Grimbo industriområde. Det är den 7.e december, i början av eftermiddagen. Det stora äventyret, båtbygget, skall börja.
Vi tas emot av Lennart Blomstergren, varvsdelägare och konstruktörson. Han visar oss var vi kan får byta kläder och var våra verktyg finns. Redan nu får vi en komplett verktygsutrustning och nycklar till förvaringsbox och skåp. Centralt finns mera sällan använda redskap. Hobbykniven får man själv hålla med.
Goda råd är nära.
Besättningen på Triovarvet utgörs av Hasse Blomstergren, Lennart, allt-i-allon Per, en snickare samt ett antal deltidsarbetande plastarbetare, så råd och om det behövs hjälp så rycker de in för att hjälpa till. Det senare visar sig behövas då och då, framförallt de första dagarna, men hjälp finns alltid att få och det känns trygga att veta. Lennart och Per har lagt skrovformens vita gelcoatlager med dess blåa snobbrand, redan innan vi kom till Göteborg, men jag har tidigare inspekterat formarna och vet att de är förstklassiga. Vi kan alltså köra igång direkt med plastningen.
Första mattlagret
Trions skrovform består av tre delar, två stora halvor och en liten avslutning på roderskäddan. Första lagret glasfibermatta är en 300 grams matta, dvs. hälften så kraftig som den 600-matta som används till det fortsatta skrov byggandet. 300-mattan läggs när formen är delad, detta underlättar arbetet betydligt och eftersom vi börjar med den mest lättarbetade mattjockleken så skall enligt alla regler jobbet gå som en dans.
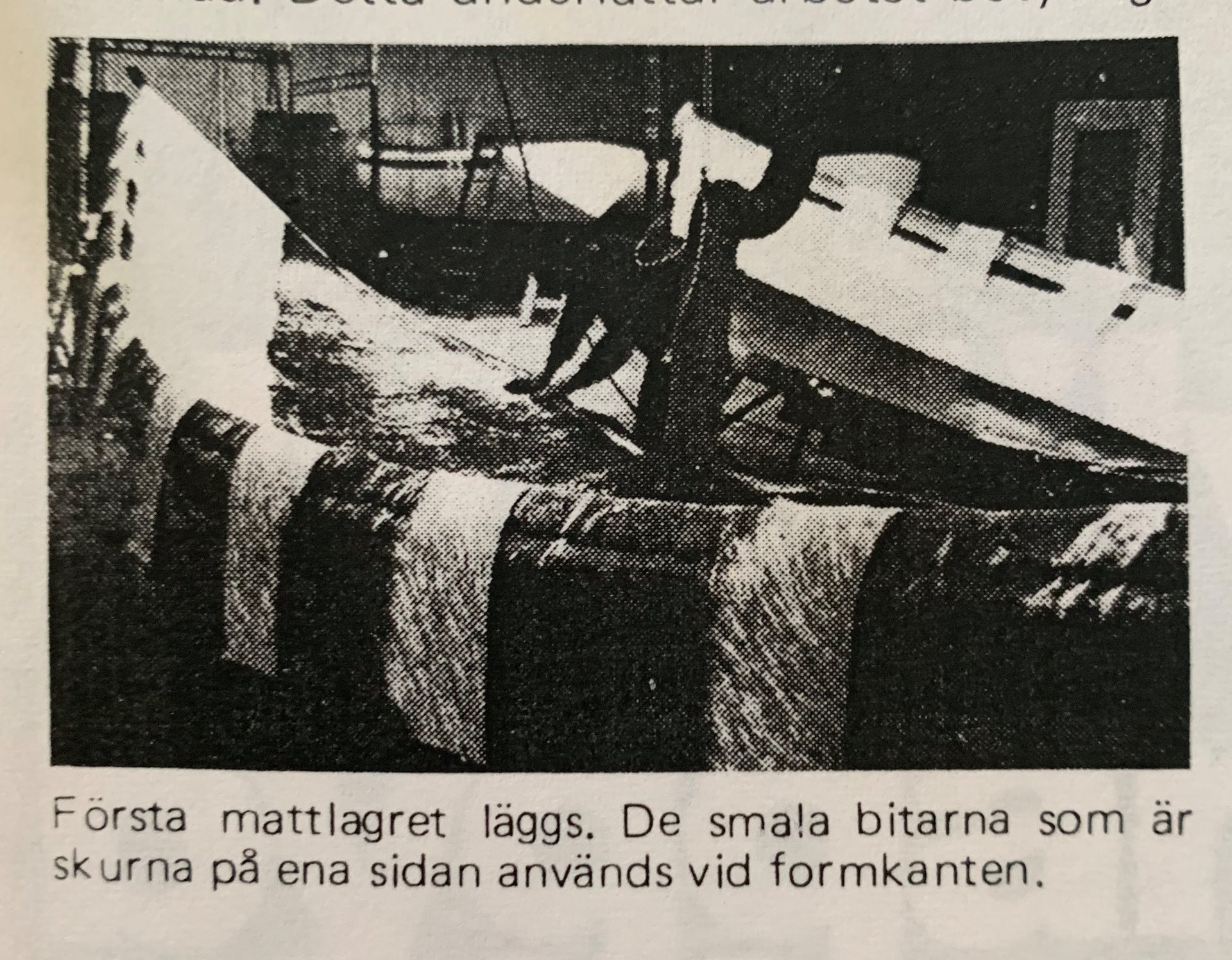
Lennart instruerar oss ordentligt och deltar en stund i
jobbet för att kontrollera att allt går rätt till. Vi blandar plast och härdare
i tioliters plasthinkar, ca tre liter plast åt gången med en procent härdare i
något som ger en härdningstid på något över en timme vid 18 grader C. Att lägga
den första mattan är ganska enkelt. En man lägger plast över ganska stora ytor
samtidigt med den största påläggaren och sedan lägger han ut meterlånga
mattbitar i plasten och rullar ut dem med påläggaren. På detta sättet
försvinner det mesta av den luft som finns under och i mattan och den som
stålrollar har inga problem att rolla ur resterande luftblåsor. Svårigheten är
att inte använda för mycket plast. Det är glasfibern som ger laminatet styrkan
och segheten inte plasten. Vidhäftningen av nästa matt- och plastlager blir
bättre om underliggande lager inte har för mycket plast. Å andra sidan får laminatet
inte vara för torrt. Men det går snabbt att lära sig ideal kombinationen plast
och matta och efter en stund hör man på stålrollerns ljud när den går över
laminatet, om plastmängden är den rätta. Rollern skall "sjunga". Är
plastmängden för stor så "klafsar" den, är mängden för liten syns det att
mattan inte blir ordentligt indränkt och rollern låter dovt.
Relingslist och kölparti svårast.
Det enda som orsakar svårigheter
för oss den första dagen är de kraftigt vinklade ytorna under " relingen" på
skrovet. Här måste vi vara noggranna eftersom luftbubblor i skarpa veck och
ytterlager lätt blir hål i gelcoaten även vid ganska lätta slag. Det är också
svårt att jobba när man är tvungen att böja nacken i 90 grader. För att se där
man skall rolla. På skarpt vinklade ställen duger bara den lilla "
enhjulsrollern", men den når å andra sidan nästan överallt. Och när den inte så
används en smal pensel att pressa ur luften med. I kölskäddan och på denna lösa
avslutning lägger vi förutom 300-gramsmattan tre lager 600-mattor. När
formhalvorna sätts samman på morgonen dag 2 så blir detta parti mycket svårt
att komma åt och därför är det viktigt att få en stark laminering här från början.
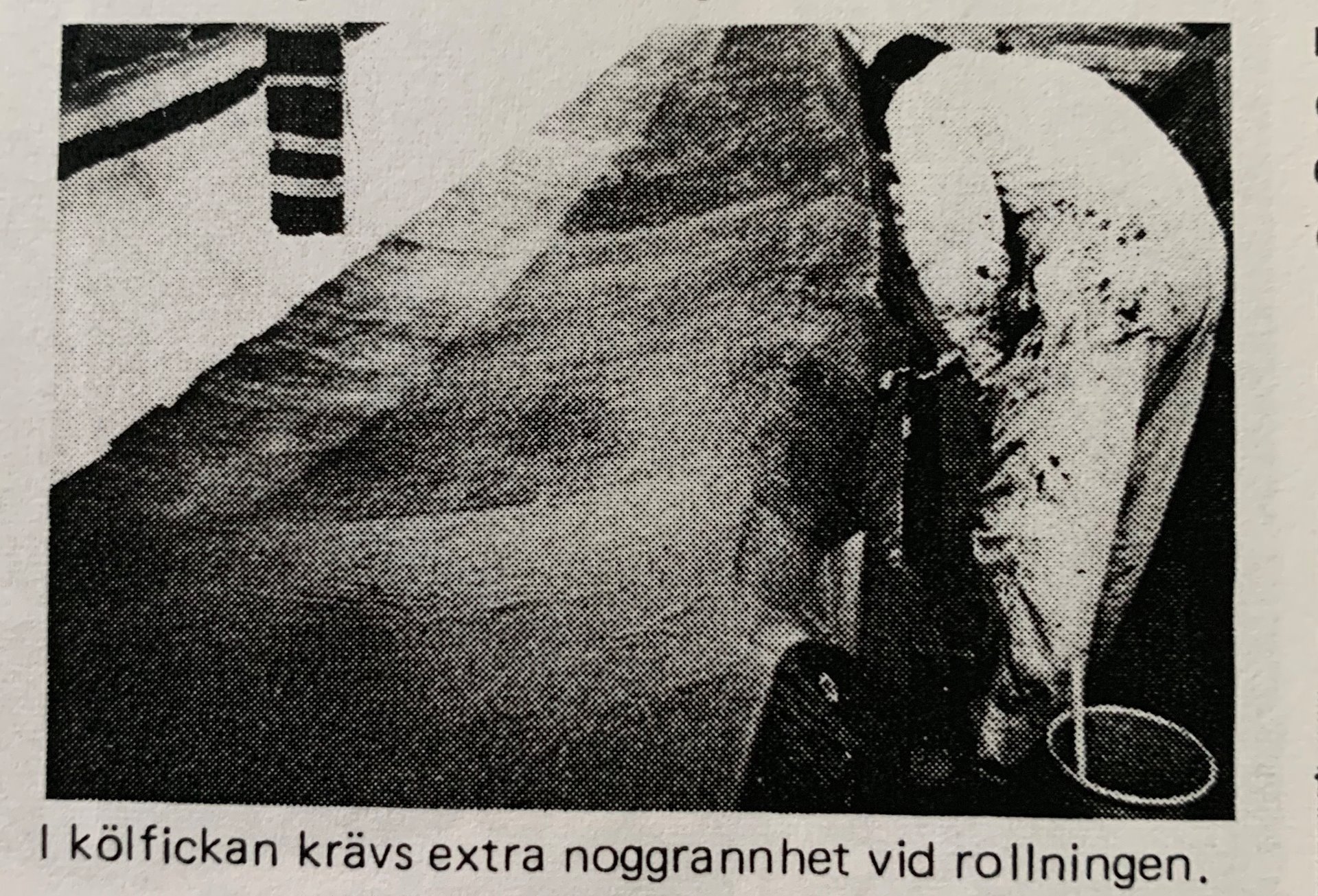
Ryggskott och styrenluft
Helt regelvidrigt arbetar vi utan skyddsmasker den första
dagen. Det gör vi för att få reda på hur man påverkas av även små styrenmängder.
Vi märker inga illamåendesymptom, men får en besk smak i munnen och när vi på
kvällen går ut för att fira det första färdiga jobbet med restaurangmiddag
smakar öl och biff styren. 5 timmar tar det
"enkla" och Snabba" grundarbetet. 17 kg plast går det åt och det ger oss ett
ganska torrt men ändå ordentligt indränkt laminat. För övrigt så ger de fem
timmarna både stelhet, träningsvärk och ryggont, något som man märker när man kravlar
ur sängen den andra plastningsdagens morgon. Huvudet känns tungt av styrenen
och i fortsättningen utförs alla jobb med skyddsmask på.
Skrovet ett grovjobb
På morgonen inspekterar
Lennart första laminatlagret, bättrar på ett par ställen och sedan sätter vi
samman och bultar ihop formhalvorna. Nu börjar det verkliga grovjobbet. Vi börjar jobba inne i
formen, som nu vilar på ena sidan. Först fyller vi upp den allra skarpaste
delen av vecken mellan formhalvorna med Micro ballonger och plast och sedan lägger
vi en dubbel remsa 600-gramsmatta över skarven och rullar ut den mycket noga.
Härefter bygger vi upp laminatet med meterlånga rivna mattbitar som får
överlappa varandra ca. 10-15 cm. Förs dränks formen in med ett lager plast, sedan
läggs matta på, dränks in och sedan en lika stor matta direkt ovanpå denna. Ny indränkning
och sedan stålrollning. För två man går jobbet ganska snabbt, men det är tungt
att rulla ut mattan med de långskaftade stålrollarna och man svettas ymnigt i
sin skyddsmask.
Att lägga två lager 600-matta över den ena skrovsidan samt ytterligare två lager i själva formskarven, där skrovet skall vara som kraftigast, tar oss större delen av dagen. Liksom tidigare ligger svårigheterna i att få ett "snyggt" lufttomt laminat under relingskanten och i kölfickans skarpa veck. I det senare jagade jag en luftblåsa fram och åter under nästan en kvart innan den gav upp. Men så är det också betydligt jobbigare att rolla ut luften ur två 600-mattor än ur en 300-matta.
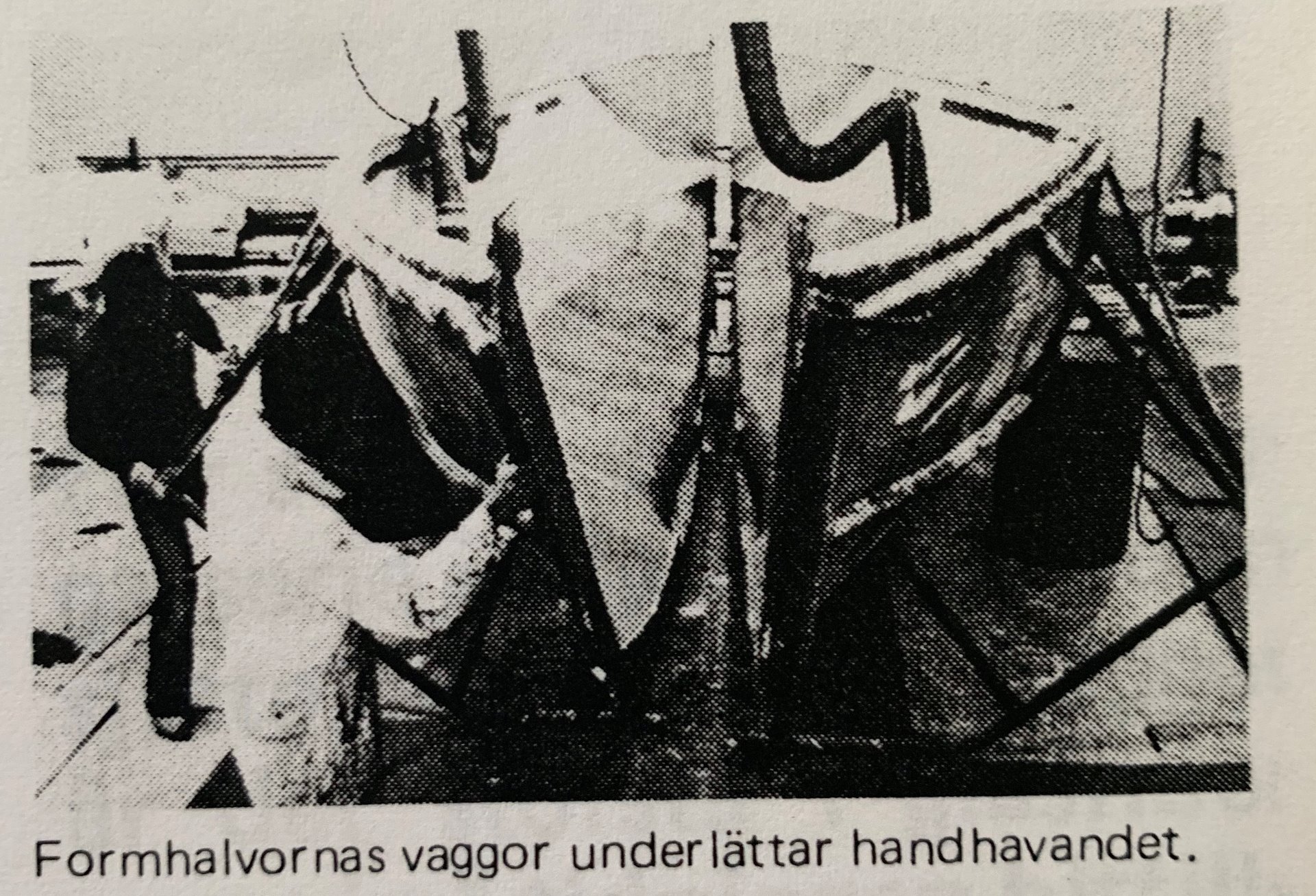
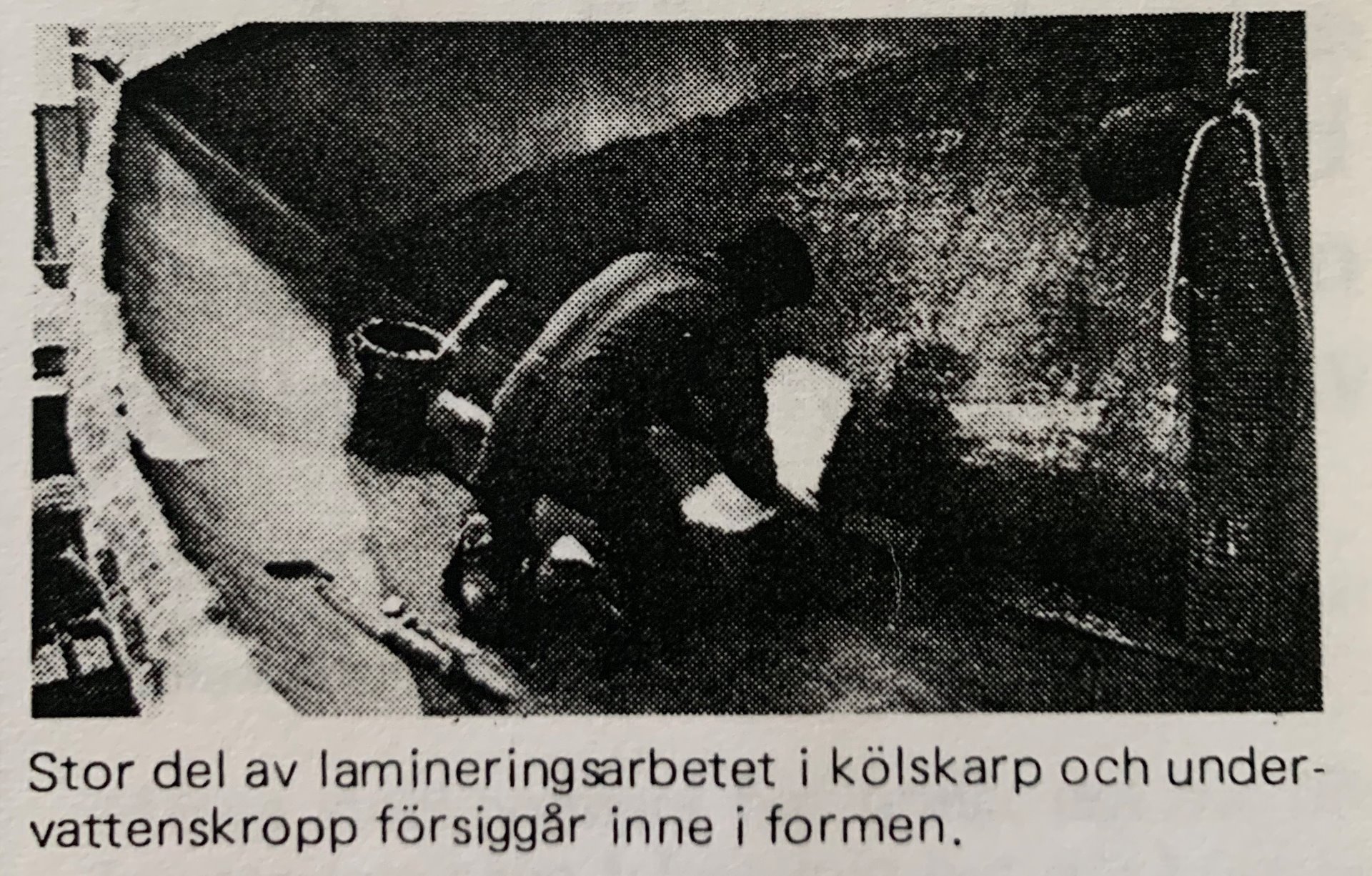
Svåråtkomliga partier.
I början av dag 3 vänder vi formen och lägger två lager på babordssidan. Varje lager matta får överlappa kölfickan och formskarven, vilket ger ett extra kraftigt bottenlaminat. Svårigheterna ligger i att jobba inne i formen, att få ett homogent laminat i kölfickan och vinklar, inklusive förspetsen, samt, innan vi lärde oss knepet, att lägga upp laminatet på akterspegeln som befinner sig i slutet av den liggande formens branta uppförsbacke.
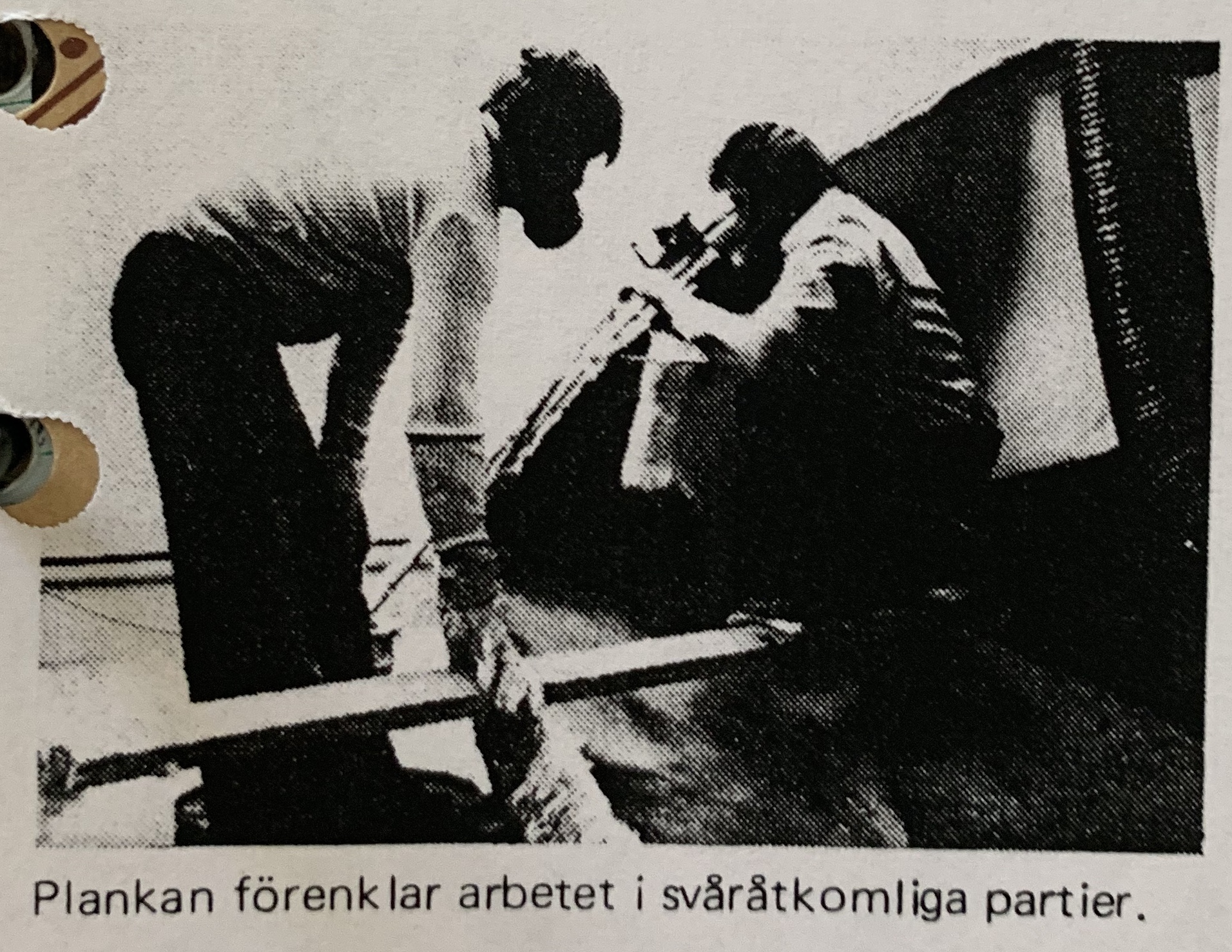
Det var förs sedan jag själv halkat i den plastslippriga formen och glidit ned över en meter, i nyss lagt laminat som fick lära oss knepet att lägga en planka från en bock utanför formen in till upphöjningen vid kölskäddan och ifrån denna planka sköta uppläggning och rolling.
Härifrån kom vi också åt att sköta det lite besvärliga
jobbet att lägga strimlor av matta ned i den trånga kölskäddan dit vi också då
och då hällde resterande plastdroppar och stoppade väl indränkta ihop kramade
små mattbitar.
Fyra dagars jobb för två.
Om vi räknar bort den första kvällens fem timmars jobb med läggandet av 300-mattan så tog hela skrovlamineringen fyra arbetsdagar för två personer. Under arbetets gång vänds former tre gånger från den ena sidan till den andra. De största problemen vid plastning är att få luft fritt laminat i de skarpa vinklarna under " relingskanten", i fören där det är trångt att jobba, och i kölfickan. Vid varje nytt laminatlager får man börja jobbet inne i formen med kölfickan. Härvid drar vi från början med oss en massa skräp under våra plastvåta skor, men sedan en man fått uppdraget som "skoputsare" när den andra går in, så löser sig problemet. Lite skräp i laminatet gör i och för sig inte så mycket bara luftblåsorna kring skräpet rollas bort.
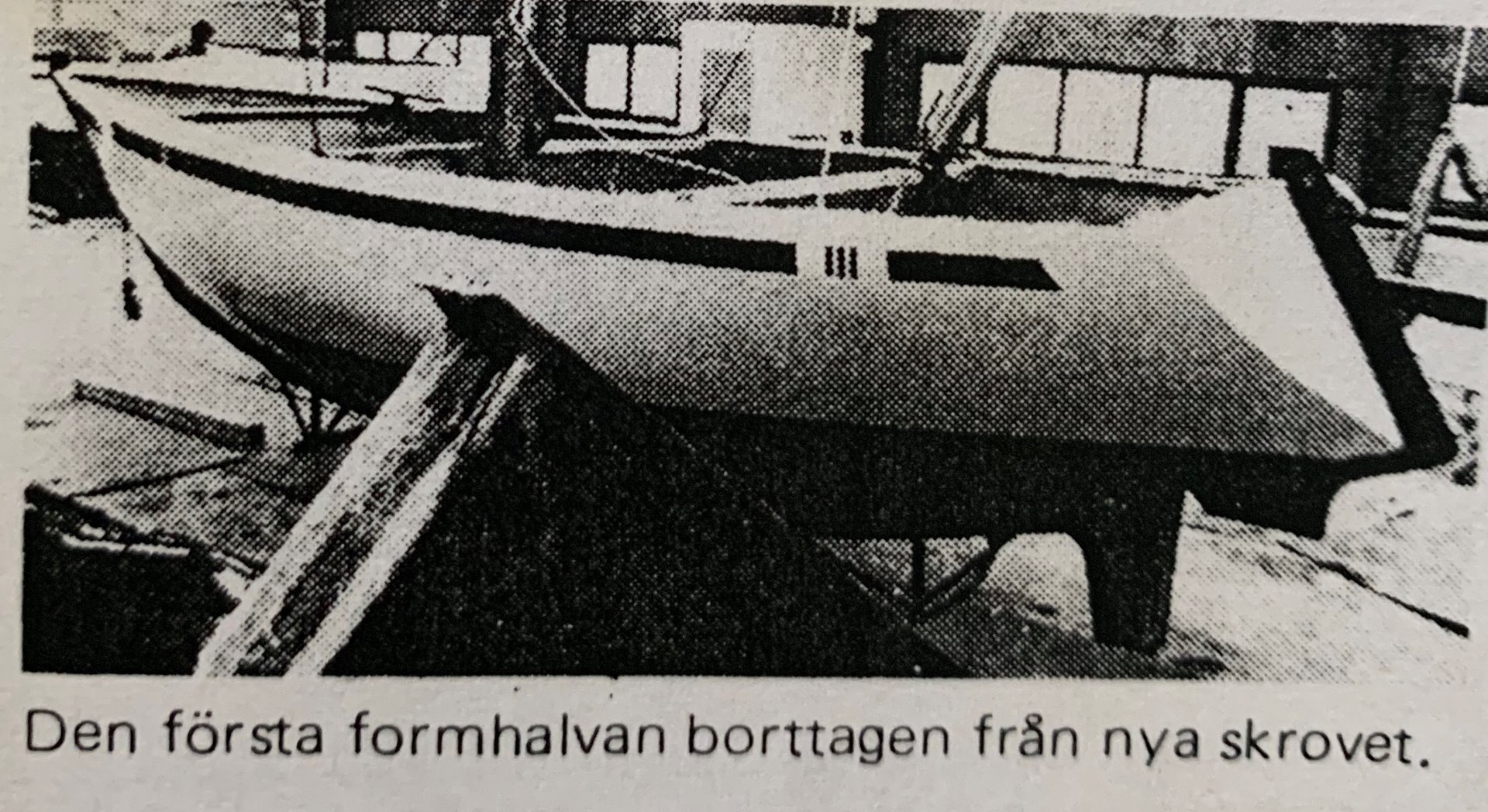
Den 12 december råder stor
förväntan på varvet. Åtminstone invid vårt bygge. Formen skall nämligen
"spräckas" och skrovet avslöjas i all sin glans. När alla bultar skruvats ur
formhalvorna lossnar skrovet med ett brakande. Vi släpar undan formarna och se
- det blev ett riktigt Trio 80-skrov, snyggt, blankt och skinande, utan synliga
brister.
Däcket en dans
Efter konstiga arbetsställningar med lamineringen av det stora skrovet så blir däcksarbetet något av en klimax. Här är ytorna visserligen både krökta och vinklade på alla möjliga sätt kring sittbrunnslådan, men det går lätt att komma åt kring samtliga delar av formen med en vanlig kortskaftad stålroller och påläggare, något som underlättar arbetet oerhört och inte minst- man får jobba ned mot en liggande form.
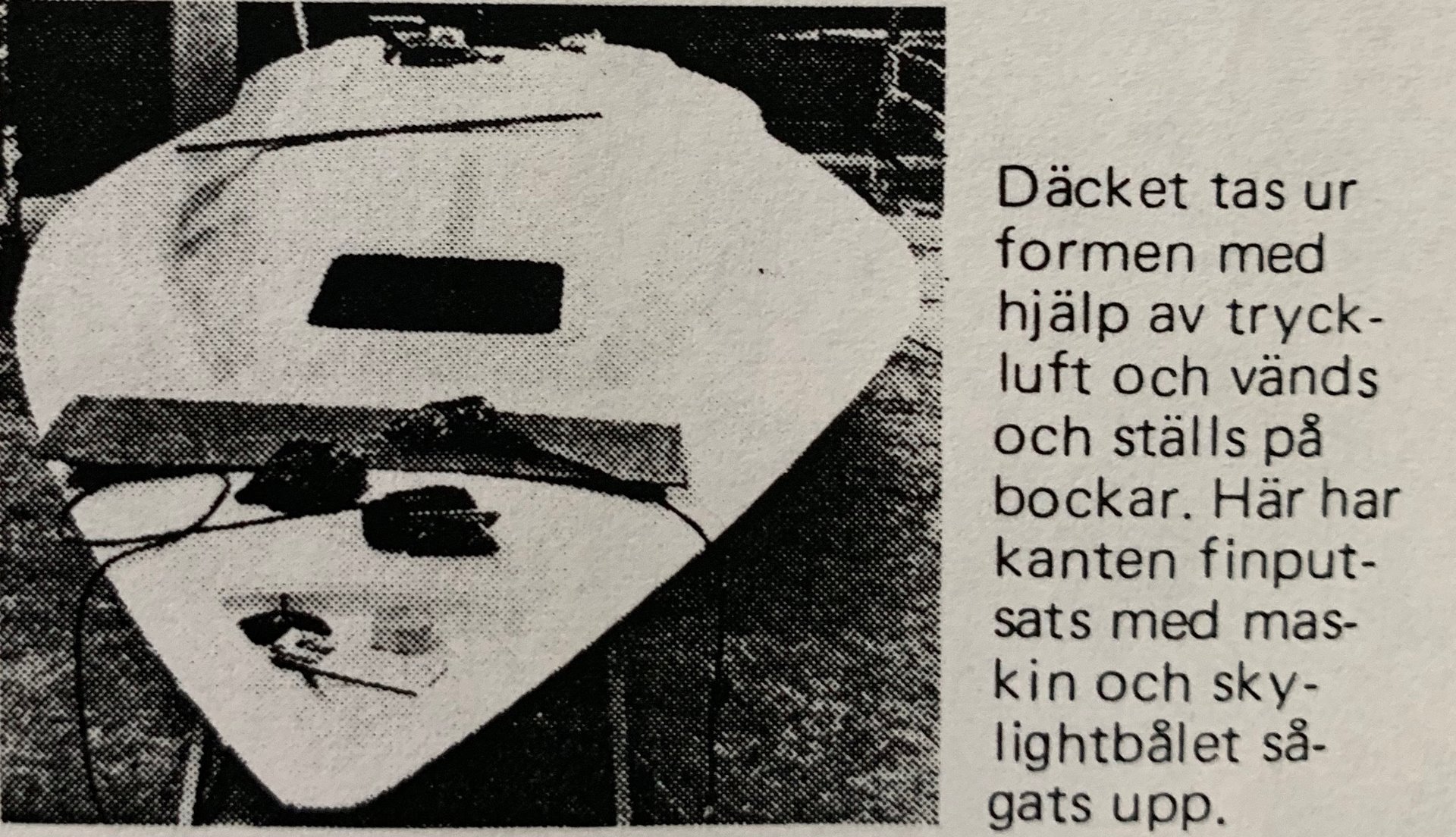
Renskär direkt
Ett tips som besparar mycket arbete är, att redan under plastningens gång renskära kantytor på formarna från överflödigt " mattskägg". Det gör man lämpligast när härdningen gått så långt att plasten börjar kännas seg. Skär man för tidigt fransar laminatet sig, skär man för sent så går det inte. Renskär också ca 4 cm av självlänsbeslagen. Här skall så småningom länsslangen fästas.
Luckorna ett sidoknäck.
Att plasta skrov och däck tog oss åtta fulla arbetsdagar, däri inberäknat de timmar som läggandet av 300-mattorna tog i anspråk. Här måste jobbet planeras så att första lagret får härda över en natt innan man börjar lägga 60-mattan.
Parallellt med skrov- och däcksjobbet passade vi på att plasta luckorna till ankarbox och sittbrunnsfack, skjutluckan till ruffnedgången och dess luckgarage samt de två "handskfacken" som fästs under sittbrunnssargen. Lucka plastningen är lämplig avkoppling när man vill räta ut ryggen efter en dust med de stora skrov ytorna. Den enda form som är lite krånglig att jobba med är luckgaragets. Här får man jobba med många små mattbitar för att få ett luft fritt laminat uppe i " vågbrytaren"
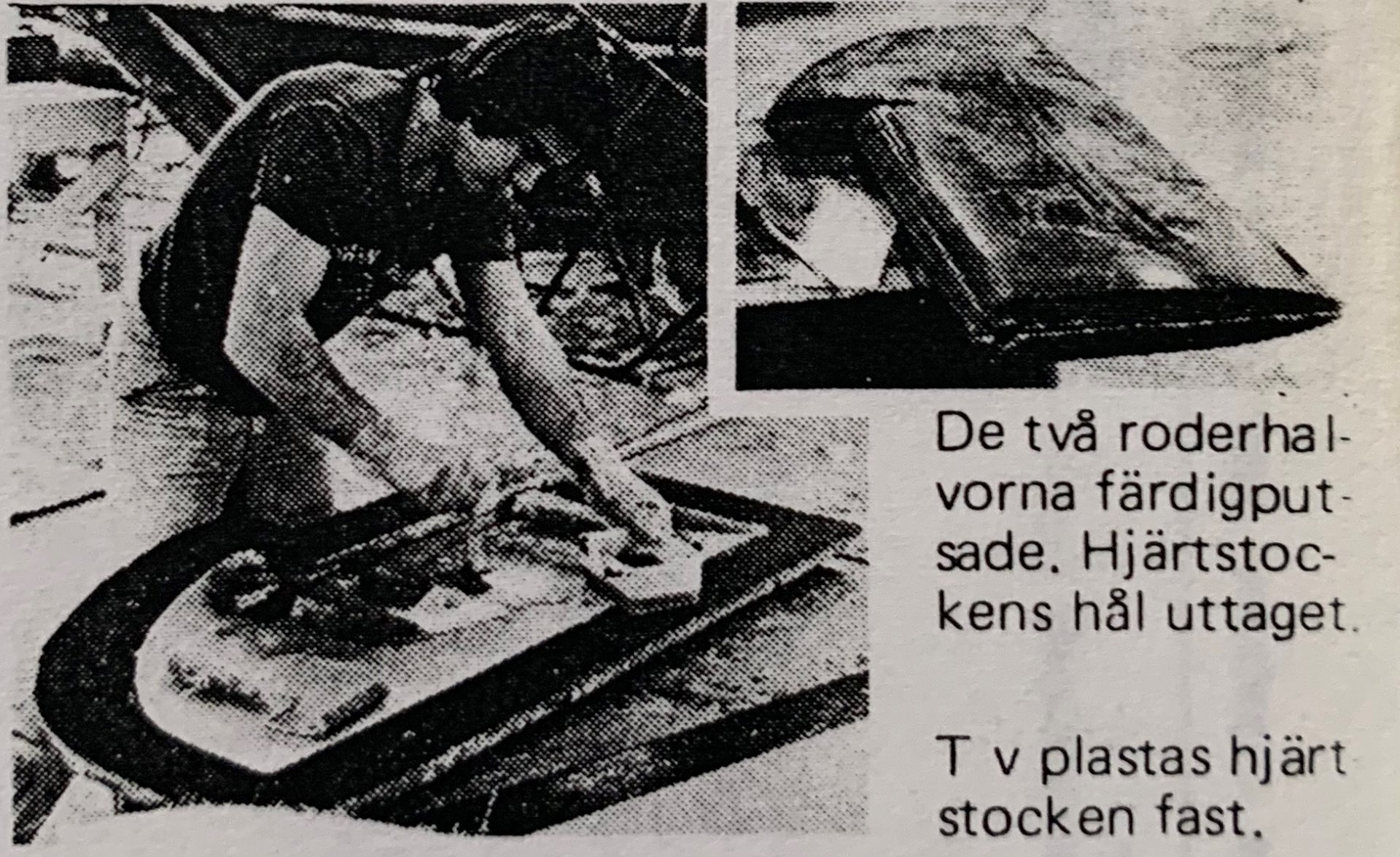
Rodret tar tid
Om luckorna fungerar som " sidoknäck" så är rodret ett heltidsjobb. Inte själva lamineringen, men den nerskärning, inpassning och filning som måste göras för att få perfekt anläggning mellan de två halvorna. Sedan de två roderhalvorna väl är färdiga och inprovade läggs hjärtstocken i rostfritt stål upp på en bädd av plast-talkblandning och remsas sedan fast med fyra-fem lager matta.
Rodret läggs sedan samman
i formen igen och fylls med plast skum. Sammanlagt krävs nästen ett dagsarbete innan
rodret är färdigt.

Noggrannhet
Med hjälp av tryckluft lösgöres däcket ifrån sin form och finputsas i kanterna med slipmaskin. Med hjälp av en skjutbar lyftställning placeras det sedan provisoriskt ovanpå det likaså finputsade skrovet. Nu börjar det hela att se ut som en båt.
Nu kan vi också summera den första periodens arbete. Vägledande har hela tiden varit ett ord. Noggrannhet. Noggrannhet med påläggning av plast och stålrollning av laminaten, extra noggrannhet med lamineringen i skarpa vinklar och djupa fickor som t.ex. roderskäddan och kölfickan och inte minst - noggrannhet vid förbehandling av dygnsgammal plastyta där ny plast skall läggas.
Miljöplasten fungerar. Standardmässigt byggs Trio 80 i
miljöplast Nordpol 44-85, från norska Jotun. En hel del kritik har riktats mot
miljöplasten främst på grund av delamineringsrisken, men trots att vi lade upp flera
laminat där vi på prov överskred de tidsgränser som plasttillverkaren satt ut
för plastning på gammalt laminat utan bearbetning(24-timmar) så lyckades vi
inte få dessa plaststycken att delaminerat ens vid hård mekanisk bearbetning,
vid plastning av skrovet sandpapprade vi och med aceton tvättade alla ytor som hade
härdat mer än 20 timmar. På så sätt garanteras en god vidhäftning. Vid samtliga
håltagningar i skrovet och däck har vi också hittat enbart perfekt laminat.
Återberättarens egna ord.
Så gick det till i Grimbo hos Trio-båtar AB.
Hur dagens båtar byggs är en annan berättelse. In Line varven är många och tidsmarginalerna små.
Men här fick du en inblick hur man byggde en härlig Trio 80.
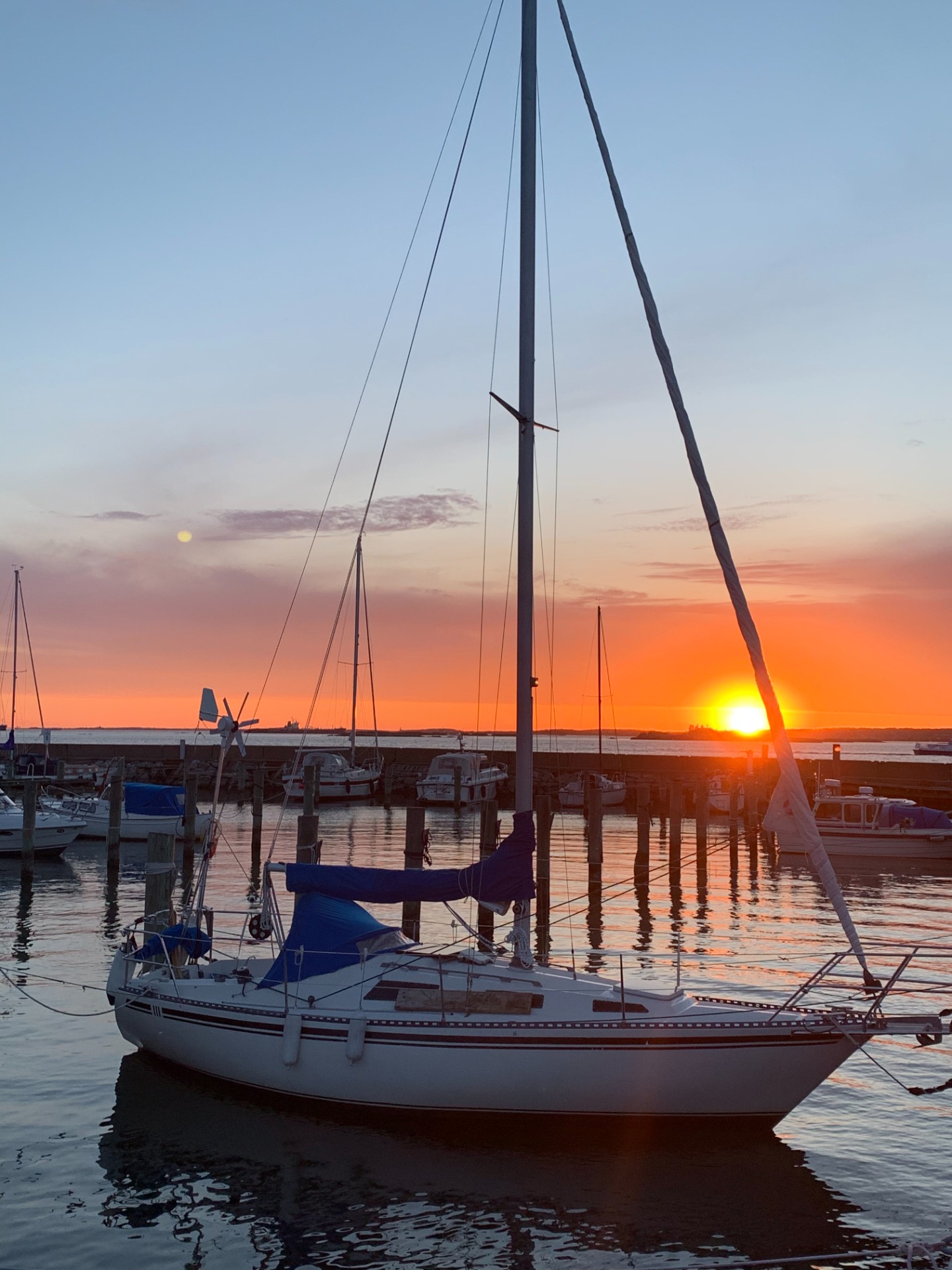
Delaminering av fördäck.
Båtar i Trio båtarnas ålder får sår och "krämpor" med tiden. Här följer en insikt hur ett fördäck som delaminerat lagas. Dock var detta en motorbåt som fått problem, men proceduren är den samma. Det är inte ovanligt att däcket på 70 - 80-talens glasfiberbåtar med tiden delamineras, vilket har skett om däcket tydligt sviktar, när man stiger på det.
Inledning.
Fenomenet uppträder vanligen mitt på fördäcket där spännvidden, och därmed påfrestningen är som störst.
Ofta kan man avgränsa det delaminerade området på ett ungefär, genom att knacka på däcket, t ex med ett mejselskaft. En dov ton indikerar själva delaminerings området. Det låter "tomt". Knacka runt och lokalisera området på detta sätt och märk ut.
För att däcket skall vara lätt, starkt och samtidigt styvt är det uppbyggt av ett sandwich-laminat. Det vill säga ett övre skikt av glasfiberplast på ungefär 5 mm tjocklek och ett undre skikt av på ungefär 3 mm tjocklek och däremellan ett distansmaterial av balsaträ eller skumplast på ca 10-20 mm tjocklek. Det övre skiktets tjocklek bestäms av att det måste tåla slag och stötar och tyngd, medan det undre är endast till att hålla allt på plats. På undersidan är det vanligen en matta för isolering påklistrad med kontaktlim. Eller så sitter detta på löstagbara plattor.
Vid tillverkningen av däcket, plastas det övre skiktet på den gelcoatade formen ( kallad plugg). Därefter plastas distansmaterialet fast i den blivande formen och slutligen plastas det undre skiktet ovanpå distansmaterialet. De fyra skikten (gelcoat, fiberplast, distansmaterial och fiberplast igen) är således fast förbundna med varandra vilket är nödvändigt för att konstruktionen ska vara styv och hållbar. När däcket blivit delaminerat har det undre eller övre skiktet släppt från själva distansmaterialet.
Delamineringen kan ha olika orsaker och kan uppstå såväl på båtar med balsaträ som med skumplast som distansmaterial. Men vanligen beror det på att vatten läckt in någonstans. Med balsaträ uppstår en komplikation. Materialet ruttnar och omvandlas så småningom till en brun smet. Skumplasten trycks antingen ihop och lämnar ett utrymme mellan glasfibern eller så pulveriseras den och släpper på det sättet.
I båda fallen samlar ihåligheten fukt och en ond cirkel är påbörjad med frostsprängningar i värsta fall. Om delamineringen är avgränsad till en del av däcket kan skadan lagas.
Det finns dock 2 skolor. Borra upp ett flertal hål, rensa ur med ex. (skaftet på en insexnyckel i borrmaskin och dammsugning) och fyll på med epoxy tills det bubblar upp i det närliggande och på detta sätt fylla tomrummet bit för bit.
Eller om man inte vill ha ett "maskinsgevärs skjutet fördäck" (Man skall vara medveten om att det kan vara svårt att få samma färg på gelcoaten om man öppnar upp ovanifrån.) kan man såga ur det undre skiktet av glasfiberplasten från insidan. Det skadade distansmaterialet rensas ur, nytt distansmaterial limmas in varefter locket av glasfiberplasten limmas på plats igen. Och fogen fylls med spackel.
Så här gjorde jag.
På min båt gamla motorbåt, en Finmar Cabin från tidigt 70-tal hade ett område på knappt en 1/2 kvadratmeter av fördäcket delaminerat. Vatten hade läckt in igenom sprickor vid pulpitfötterna framme i fören. Så jag tog mig slutligen samman och reparerade delamineringen.
Jobbet var tidsödande men inte svårt. Det fordrar dock eftertanke och planering.
Jag valde att öppna däcket underifrån, då däcket dels hade en förhöjning mitt på som skulle vara svår att återställa. Och den blå färgen skulle vara omöjlig att återställa. Så här i efterhand anser jag att det också var lättare att arbeta från undersidan, eftersom däckets undre plastskikt är slätt. Men på grund av den undre plastens ringa tjocklek kändes den ömtålig för att kunna användas som mothåll vid reparationen. Sedan är det lättare att dölja fogen under isoleringsmattan om den inte skulle bli så snygg.
Arbetsställningen är minst sagt obekväm. Jag valde att arbeta med epoxi som visserligen fordrar stor noggrannhet vid tillblandningen och är kletigt men som annars är lätt att använda både för laminering och vid spackling. Epoxi är mycket starkt. Materialet och distansmaterialet Divinylcell köptes jag hos Sea Sea Båttillbehör AB, men det finns också andra ställen, till exempel hos Erlandssons Brygga. Genom provborrningar från undersidan fastställdes att ungefär 0,50 kvadratmeter av fördäcket var skadat. Balsan var rutten. Isoleringsmattan på insidan slets bort, varefter området skars ut från undersidan med en vinkelkap som ställts in på ett djup av en halv centimeter.
Den lösgjorda skivan kunde nu med lite bändande lyftas ut som ett lock tillsammans med balsamaterialet. En del av träet hade ruttnat till en blåsvart smet. Plastlocket, däckets undersida, var väldigt tunt plastad (1-1,5mm) så jag plastades upp en ny skiva, till en tjocklek på 3 mm.
Enklast skedde detta på ett par ark stadig polyeten utlagd på en plan formplywood .Efter ett dygn kunde den härdade, nya skivan sågas till efter den gamla delen. Här ska nämnas att epoxi kräver en speciell kvalitet av glasfiber. Det går således inte att använda den vanliga typen av matta och väv avsedda för polystyren.
Undersidan på däckets övre plastskikt skrapades ren från balsarester varefter den slipades med grovt sandpapper. Så fick all fukt torka ut under ett par veckor med värmefläkt och en avfuktare som gick tills minimalt med vatten fanns i behållaren. Detta krävde en del koll de första dagarna. Det skall även nämnas att ruffen stängdes till för att få ett så tillslutet utrymme det gick, för att inte få in ny fukt.
Som nytt distansmaterial valde jag Divinylcell med en tjocklek på 10 mm. Materialet kom i skivor på en kvadratmeter med gles glasfiberväv. Det var lätt att skära till för att passa i hålet med den utsågade skivan som mall.
Så var det dags att fästa fast det hela. Ett arbete som bör planeras noga. Med ett spackel fäste jag Divyinylcellen mot fördäcket. Nu måste det gå fort, inte för att det utstrukna spacklet härdar särskilt fort, utan för att spacklet tar värme i blandningsburken och börjar stelna efter en halvtimme. Det är således klokt att blanda mindre mängder ett par gånger i flera burkar under arbetets gång i stället för att starta med en stor sats direkt.
Spacklet är mycket lätt att arbeta med, även uppåt. Ett lager appliceras med spackelspade på alla ytor och på den undre skivan, på distansmaterialets båda sidor och på undersidan av däckets övre skikt.
Distansmaterialet läggs på den undre skivan och kakan trycks upp i hålet mot undersidan på däckets övre skikt. Spacklet häftar visserligen så bra att alltsammans förblir hängande, men för att garantera god vidhäftning måste kakan stämplas fast med stöttor mot britsarna i förpiken. Det behövs ett flertal stöttor, och längsgående plankor som fördelar trycket jämt, varför dessa bör kapas till i förväg.
Spacklet avger inga ångor men sörj för väl ventilation ändå och däremot är det inte alls bra att få det ohärdade materialet på huden eller i ögonen. Man måste därför skydda sig med glasögon och rätt typ av handskar.
Stämplingen måste även ske med en viss eftertanke. Tar man i för mycket kan hela däcket lyftas till en puckel. Ett sätt är att få mothåll genom tyngd från ett par hinkar med sand.
Efter ett dygn med 18-20 grader i luften hade plasten härdat och fogen kunde spacklas igen med en ny liten sats spackel. Efter ytterligare ett dygn täckte jag dessutom fogen med två lager remsor av glasfiberväv. Efter avslipning kunde en ny isoleringsmatta limmas på plats och allt är därmed klart.
Däcket är nu stumt när man går på det och vet man inte om skadan så ser man inte ingreppet. På insidan syns den nya isoleringsmattan i taket mot skrovsidornas lite mörkare men det är marginellt. Skadorna vid pulpit fötterna lagades också men det är en annan historia. Nu har den båten ett stabilt däck att gå på..
Patrik.
Här följer en bra broschyr från NM-plast med bra information vid epoxi- arbeten.